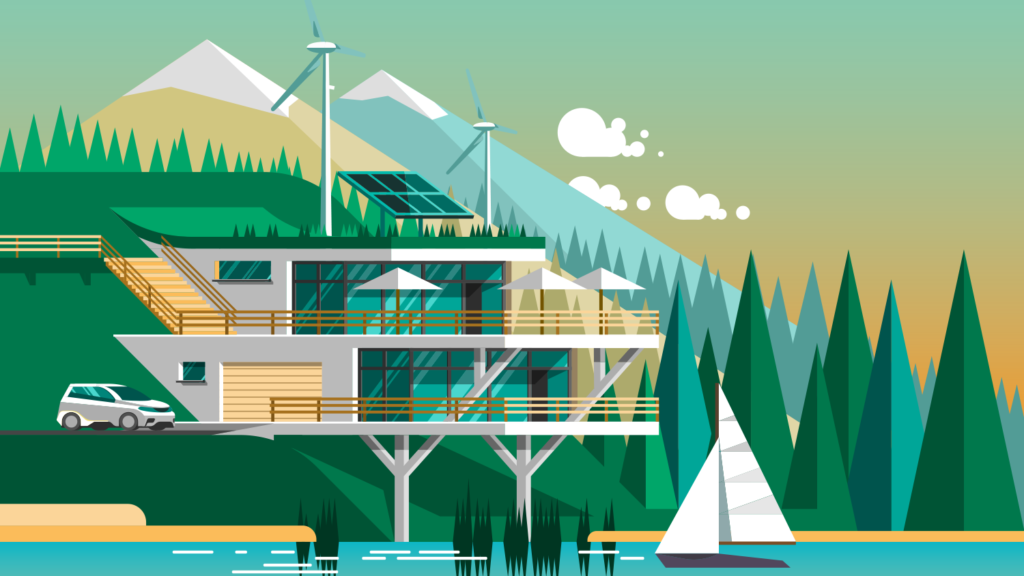
From building to operations
In recent years, extreme weather conditions have been observed around the world, with ‘once-in-a-lifetime’ natural disasters becoming yearly occurrences. The destruction of our planet as a consequence of serious carbon emissions has become an urgent issue globally. Therefore, accelerating the decarbonisation process is the top priority for everybody everywhere. William Chan of Arup looks at how climate neutrality can be built into our industries from the ground up.
Government policy on carbon emissions
Over the past 30 years, extreme weather leading to natural disasters have been taking place more frequently than before. This growing evidence of climate change, which is threatening human survival, is alarming many in society. To overcome this challenge, companies at all stages—from building construction to manufacturing—need to develop an effective carbon neutrality roadmap.
On the governmental side, more than 190 countries have promised to achieve the goal of net zero emissions by mid-century to limit global warming in this century within 1.5°C. China has announced its national target of reaching carbon peak at 2030 and carbon neutrality at 2060. The Renewable Energy Law has been published, which promotes utilisation of renewable energy and is aimed at increasing energy supplies, improving energy infrastructure, monitoring the safety of energy generation, and protecting environment – all of which are realise sustainable economic and social development. The European Union(EU) has published its Green Deal and enacted a Climate Law targeting a reduction in net greenhouse gas emissions of at least 55 per cent by 2030 compared to 1990 levels, carbon neutrality across the EU by 2050 and negative emissions beyond 2050.
According to research done by International Energy Agency, 38 per cent of total global carbon emissions comes from building sector operations and materials while 32 per cent comes from the industrial sector. Therefore, developing net zero carbon buildings and green factories can contribute up to 70 per cent of global decarbonisation actions.
Net zero carbon buildings
To understand net zero carbon buildings, the concept of ‘whole life cycle’ carbon emission must be comprehended. Whole life cycle carbon emissions are comprised of embodied carbon and operational carbon. Embodied carbon is generated during the extraction, transport and production of raw materials; and the use of materials during construction, maintenance and renovation as well as demolition at the end of the building’s life. Operational carbon is generated during the energy consumption, renovation, maintenance and waste disposal that take place while the building is in operation. When the whole life cycle total carbon emission of a building can be balanced against the renewable energy generated on site, it is defined as net zero carbon.
Green factory
Similar to building construction and operation, in order to be green, a factory should also consider decarbonisation from a whole life cycle perspective, starting from site construction to daily manufacturing streamlines.
As it remains uncertain in many ways how government carbon policies will be implemented, each corporate should select the most efficient decarbonisation roadmap for their individual situation. The roadmap should integrate their business model, development strategy and investment plan with changes to local laws and regulations, cost trends in carbon trade, availability of a local renewable energy grid, the green finance market, and so on. It should not only cover current market conditions, but more importantly, it should be able to forecast long-term developments, ideally up until 2060.
Particularly for the manufacturing sector, the costs generated by the decarbonisation process every year will greatly influence a corporate’s annual profit, so a precise tailor-made roadmap with foresight on future carbon policies, energy costs and carbon trade is essential.
A green factory development roadmap can be worked out by incorporating the below elements:
- Adopt a decarbonised energy strategy that is integrated with the corporate business model assessment.
- Apply a circular economy approach to reduce material use during (a) product manufacturing; and (b) construction, operation and demolition of building assets.
- Adopt energy-efficient equipment, such as heat recovery, energy storage and digital energy monitoring tools.
- Adopt big data, artificial intelligence machine learning tools and an Internet of Things platform to optimise manufacturing streamlines, and to facilitate building automation and digital asset management.
- Utilise low-carbon transportation throughout supply chains to decarbonise and improve the corporate environmental impact footprint.
- Adopt low-energy landscaping on-site and the surrounding area to incorporate the available natural ventilation and lighting features.
- Create and contribute to an inclusive, equitable and just society.
As an example, a food manufacturing giant promises to achieve carbon neutrality by 2035 and implements a sustainable food production lines. The factory facilitates circular economy in the production process, and equips itself with on-site wind turbines and solar farms to generate renewable energy, in order to achieve a whole life cycle net zero carbon footprint.
A wish for the future
Society should not only to aim for net zero carbon, but more even further towards negative carbon. By catching future developments in carbon technology and the digitalised world, we can install carbon-sequestering materials to absorb carbon from the atmosphere, plant green spaces in all living environments, use powerful IoT platforms to precisely control emissions, connect to fully renewable national power grids, and adopt the highest ratio of recycled and recyclable materials possible. Eventually, we will build our negative carbon world together.
Dedicated to sustainable development, Arup is a collective of 16,000 designers, advisors and experts working across 140 countries. Founded to be both humane and excellent, we collaborate with our clients and partners using imagination, technology and rigour to shape a better world.
William Chan is associate director, East Asia Science, Industry and Technology leader and Chongqing Office leader at Arup. He has extensive experience in design, site supervision and project management in the commercial sector in Hong Kong and Mainland China. He has dedicated much effort in recent years to integrate skills relating to building sustainability and digitalisation.
Recent Comments